A high-risk activity during the life of any underground mine is the use of explosives in both development and production firings. Multiple factors, primarily focused on operator safety, come into play when handling, firing, and re-entering areas where explosives have been used.
Dyno Nobel have released the second generation of their industry leading centralised blasting system, BlastWeb II, incorporating new technologies, including the ability to communicate through encrypted networks via a wide range of mine communication infrastructure (e.g. Wi-Fi, fibre and LTE) and firing the full suite of initiation systems used underground.
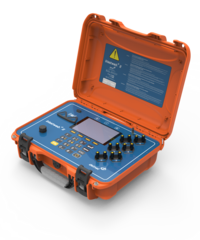
The focus of Dyno Nobel together with their partner DetNet when developing the original BlastWeb solution was to fully remove all personnel from the underground environment during and immediately after firing time. Working with some of the world's deepest mines in South Africa, the solution was developed and tested in extreme conditions, and proven at a surface-based firing point, over 3 km from the initiated blast.
"Our customers were keen to remove all operators from the underground operations and then control blasting from a central location. This was the starting point for the first BlastWeb system," outlines Nico Swart, Technical Specialist at Dyno Nobel.
"The major step forward for us with BlastWeb II is the ability to control, initiate, and have full visibility of all electronic detonators connected underground. Production firings underground have moved largely to electronic detonators (both wired and wireless), so the capability to control both these and traditional explosives (e.g. Nonel®) fired by a DriftShot® Starter and detonating cord from a centralised blasting system became essential."
BlastWeb II's continuous connectivity through multiple communication mediums enables Mine Control operators and blasting crews to progressively identify areas ready for end-of-shift blasting. This aids pre-blast preparations, adds the ability to conduct real-time blasting schedule assessments and remote updating of the firmware on the installed Blast Control Units (BCU) underground.
Beyond the improved visibility and control of the system, there are multiple other technological developments that have delivered improved safety and operational efficiency in the latest BlastWeb II offering.
"Safe delivery of digital systems now extends beyond the usual human-driven safety factors, and we have invested heavily in cybersecurity," outlines David Gribble, Vice President Product & Technology at Dyno Nobel.
"We have incorporated multiple internal fail-safe mechanisms and improved data security within the whole system. The Surface Blast Controller (SBC), which is generally placed well away from the active mining area, has been redesigned to enhance the user experience allowing customisation to user specific requirements. Security has been enhanced with the Blast Controller now requiring Multi-Factor Authentication (MFA) to proceed with the blasting process."
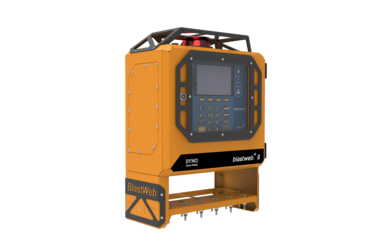
This MFA process coupled with improvements in cybersecurity gives peace of mind for full control of blasting activities and prevents unauthorised access or intrusion to the BlastWeb II system.
The technology that is applied at the underground workings and connected to the SBC has also been given a major overhaul in the BlastWeb II iteration.
The BCU, which can either be permanently installed or mobile depending on operational requirements, has moved forward with increased capacity and range.
"We can place multiple BCUs around the underground network, whilst interconnected to the same SBC. This network will then in real-time update any status change before or during firing activities. The inclusion of NFC technology for activating the BCUs when an area is locked down for blasting at any time during the shift removes the requirement for blast crews to return to the area. Further to this visibility, we can easily increase the scale of blasting operations as we can now use BCU to BCU connections to effectively interconnect units as required. This allows us to load large production firings, or fire simultaneously over multiple working areas, that sometimes can exceed two thousand detonators" explains Gribble.
This adaptability and scale in the rugged underground environment are valuable due to the ever-changing nature of operational requirements. For customers with existing BlastWeb systems the BlastWeb II equipment is backwards compatible and can co-exist on the same network. The system also offers added value in its ability to network with other digital systems near blasting activities.
"The BlastWeb II solution offers an integration which enables connections to the secondary ventilation system. This allows on/off control of the fans post-blast to ensure that ventilation is available to an area immediately post-blast, aiding quicker re-entry activities and a safer work environment for those working underground," shares Swart.
Dyno Nobel has a rich history in delivering and innovating commercial explosives, continually enhancing its solutions to adapt to the modern underground environment. The BlastWeb II solution notably enhances safety, visibility, performance, and the repeatability of blasting activities for underground operations.