Weir has developed a range of transformational flowsheets for tailings management to help miners reduce, rethink, and repurpose their tailings. Weir recognises that its customers have different requirements and different constraints, and its flowsheet-based approach allows it to partner with miners to understand the advantages and disadvantages of each solution and provide a balanced assessment of each approach.
Weir realises that, as an original equipment manufacturer, its tailings management solutions can't simply be dictated by its product portfolio. Through consultation, it comes to understand the constraints of each operation – water, energy, carbon and existing footprint, for instance – and focuses on designing and validating the best solution to combat these challenges and deliver operational and structural stability.
Essentially, the transformational flowsheets Weir has developed provide a starting point to explore a full suite of tailings management options. They're all customisable, ensuring each operator is able to arrive at the optimal solution based on their needs and objectives.
Two innovative solutions – Terraflowing and coarse particle flotation (CPF) – described below are changing the way miners manage their tailings. At the same time, Weir is also developing new technologies to complement its transformational flowsheets.
Terraflowing
Terraflowing is a dewatering process in which discrete tailings fractions are handled in a way that produces an engineered paste product. The process can change based on the site's requirements, utilising a range of technologies that can include cycloning, screening, paste thickening, filtration and decanting, amongst others. At the same time, it isn't restricted to the use of any specific technology.
By separating the tailings stream into discrete fractions, operators can handle them in different ways, providing a higher level of flexibility in the way they dewater their tailings, while still having a consistent end product.
This allows operators to do different things with these discrete fractions (eg, reprocess them, utilise them for backfilling, etc) or recombine them later in the process. They can then be pumped to the tailings storage facility (TSF) for deposition.
This approach delivers operational stability, despite input variations. Moreover, the resulting engineered product is more stable, which is better for maintaining the structural integrity of the TSF and, as a result, protecting the surrounding environment.
In contrast, traditional dewatering circuits are susceptible to variations in both feed and process conditions. Consequently, the TSF design must account for potential fluctuations in product properties. In contrast, the Terraflowing process delivers an engineered paste product, providing operators with a more versatile dewatering solution.
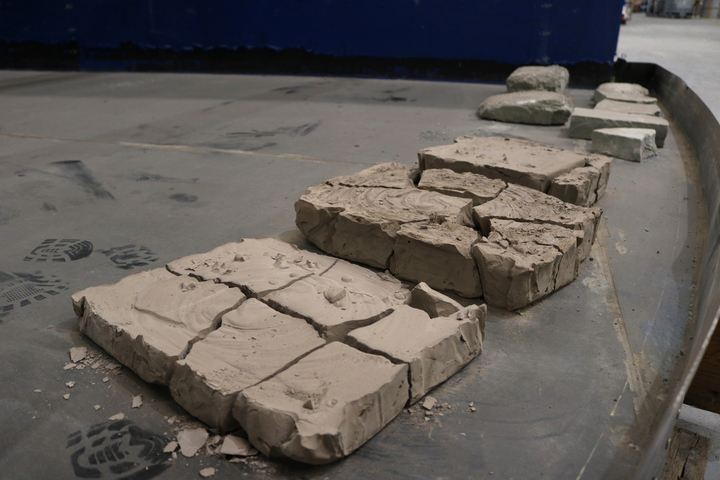
Coarse particle flotation
Coarse particle flotation (CPF) can be used in two ways: in the mill circuit or in the tailings circuit.
To ensure it can offer this technology to its customers, Weir has a cooperative agreement with Eriez, allowing them to collaborate and apply its HydroFloat® CPF technology when it's the ideal solution.
Utilising CPF in the mill circuit allows miners to remove approximately 30-40% wt/wt of the total gangue at coarse fractions (150µm) in the early stages of the process. This allows operators to reduce energy consumption in traditional semi-autogenous grinding/ball milling circuits by 30-50% (with further reductions achievable by replacing ball mills with high pressure griding rolls) and produce coarse tailings that facilitate improved water recovery and tailings management.
In tailings scavenging (TS) applications, CPF provides selective recovery of semi-liberated and fully-liberated minerals contained within the coarse size fraction of rougher flotation tailings, thereby increasing recovery at existing grind sizes. However, CPF can more optimally be used to balance metal recoveries and grind size/throughput in this same application within the limits of an existing concentrator design.
Through the production of a coarse tailings fraction, operators can utilise such material for dam wall construction if, for instance, the operation needs to expand its TSF capacity. In CPF circuits, the coarser material is removed with, say, a Cavex® DE hydrocyclone or through conventional cycloning and screening to create a coarse flotation feed with relatively free-draining characteristics suitable for dam wall construction.
Weir Technical Centres
Weir Technical Centres (WTC) play a vital role enabling Weir to partner with miners to test various flowsheet concepts. They are centres of excellence, where various technologies and solutions for tailings management can be developed, trialled, and assessed.
The WTCs can carry out extensive testing and analysis to identify ways to optimise tailings processing methods, reduce the amount of tailings generated and ensure it's a more manageable product.
Providing proof of concept for tailings solutions ensures that any recommendations made by Weir are substantiated with practical demonstrations that can be viably scaled up and remain effective.
Weir also carries out sample testing, which includes a detailed evaluation of the pros and cons of proposed flowsheet solutions with a focus on the practical applicability in real-world scenarios.
These capabilities allow Weir to partner with miners to share its technical expertise, allowing miners in turn to make decisions about their tailings management solutions based on solid evidence and, as a result, ensuring a higher chance of successful implementation.