Mining operations consistently strive to identify process inefficiencies, improve equipment reliability, optimise the use of water and energy, and ensure the safety of people and processes. These goals are essential for maintaining operational excellence, meeting regulatory expectations, and positioning for long-term sustainability and profitability.
Faced with these challenges, leading mining organisations have turned modern technologies that unify traditionally separate process control, power systems, and digital solutions into one intelligent architecture.
The Case for Unified Architectures and Integrating Process and Power
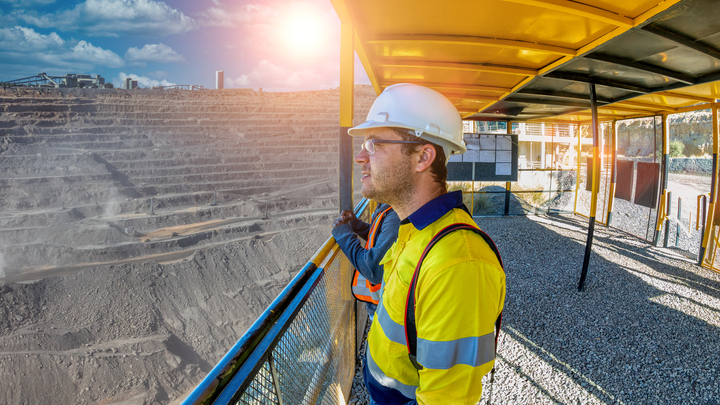
Traditionally, subsystems such as process automation, motor control, power control, networking, cybersecurity, asset management and advanced process control (APC) software operate in isolation throughout the mine lifecycle—from design and execution to operation and maintenance. This fragmented approach results in:
- Limited visibility and disconnected data: Information is locked in silos, hindering root-cause analysis, continuous improvement, and autonomous action. By unifying these systems cost savings up to 20% have been realised.
- Complex interconnection between systems: Delays project timelines and elevates operational risk as additional overheads are added to engineer and develop solutions. Timelines have been shortened by nearly 30% through simplified engineering and unified control.
- Workforce inefficiencies: Separate teams with specialised knowledge reduce the impact and scale of the impact that they can make to operations, complicating resource optimisation.
By unifying process and power domains, mining companies can standardise hardware and software, enable site-wide configuration consistency, and establish a single source of operational truth. This integration enables seamless data flow—from pit to plant to enterprise—supporting machine learning, analytics, and continuous improvement.
An integrated control strategy allows for comprehensive energy and process analytics, optimising WAGES (Water, Air, Gas, Electricity, and Steam) consumption and automating reporting. This unified approach supports smarter, greener decisions without production loss, detailed monitoring of power consumption across operations, and enables automated energy reporting for sustainability tracking.
To overcome these challenges and create an infrastructure for a truly connected mine, mining companies need a modern process control technology that delivers smart mine-wide control.
Beyond Integration: The Power of AI and Advanced Process Control
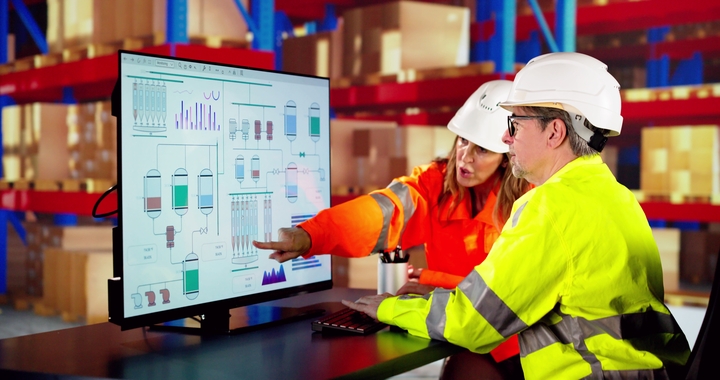
To meet the demands of modern mining, automation systems must extend beyond basic control loops. This is where AI-driven analytics and advanced process control come into play.
- AI-Assisted Engineering: Engineers can now generate standard logic sequences for conveyors, pumps, or feeders using natural-language prompts. This accelerates project delivery, reduces errors, and allows skilled personnel to focus on higher-value tasks.
- Predictive Control in Real Time: APC solutions use machine-learning models to autonomously infer critical variables like ore moisture or slurry density, automatically adjusting parameters. This stabilises throughput, boosts energy efficiency, and improves mineral recovery.
- Proactive Asset Health: AI-driven anomaly detection tracks equipment performance, such as motors, drives, bearings, against historical baselines, flagging potential issues early to avoid unplanned downtime and reduce maintenance costs.
Case Studies on Modern Process control
- At a greenfield high-purity minerals processing plant in Western Australia, the PlantPAx system facilitated seamless integration of process, power, and information systems. This strategic approach aimed to achieve a 20% cost savings and a 29% reduction in the project schedule during the commissioning phase. The unified control system streamlined engineering processes and reduced complexity, enabling faster time-to-market and substantial cost efficiencies.
- A copper mining operation implemented the PlantPAx system to integrate process control across their facility. This integration led to a 5% increase in system efficiency and a 10% reduction in utility costs. The advanced process control enabled more precise management of operations, contributing to these significant cost reductions and efficiency gains.
- At a bauxite mine in Australia, the use of PlantPAx for mine-wide control and FactoryTalk® software for real-time data access improved operational efficiency and safety. The integration of Allen‑Bradley® controllers and mobility tablets facilitated seamless control and data sharing, contributing to the project being completed ahead of schedule and under budget. This approach underscores the benefits of advanced automation in enhancing mining operations.
PlantPAx® DCS from Rockwell Automation for Modern Mining
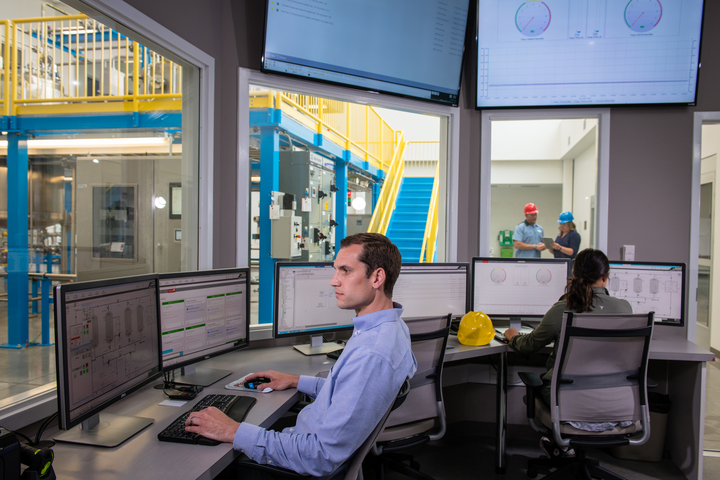
With decades of mining industry experience, Rockwell Automation delivers a modern distributed control system (DCS) that integrates process, power, and analytics with built-in AI capabilities:
· Single, Scalable Platform: From small upgrades to multi-site standardisation, allowing for flexibility and a system that grows with your operation.
· Integrated Process and Power: Unlike traditional DCS systems that separate process and power control, PlantPAx integrates them seamlessly and combines IO, instrumentation, networks using a low-code/no-code framework. This includes smart libraries for third-party intelligent power devices such as Protection Relays and Digital Trip Units that support IEC 61850.
· AI-Ready Architecture: Embedded analytics and machine-learning tools streamline engineering, stabilise processes, and predict failures before they happen.
· Robust Ecosystem: Global support, comprehensive cybersecurity features, and extensive training resources help ensure long-term success.
· Sustainability-Built: Fully integrated power monitoring and energy analytics simplify meeting decarbonisation goals and complying with environmental regulations.
Smart, unified process control is revolutionising mining operations. By adopting the PlantPAx system, companies can enhance efficiency, reduce environmental impact, and future-proof their operations.
Discover how your mine can achieve system-wide optimisation with Rockwell Automation here.
ABOUT THIS COMPANY
Rockwell Automation
HEAD OFFICE:
Level 1/248-252 Burwood Road
Hawthorn, Victoria 3122