In keeping with its mission to drive sustainable productivity, full flowsheet technology and service supplier to the global mining industry, FLS offers tailings solutions for all mine conditions. As well as working to increase efficiency, each new development the company introduces into the tailings management arena is designed to improve safety, reduce risk and minimise environmental impact.
A major development on this front comes in the form of the AFP2500 automatic filter press, which incorporates innovations focused on reducing the total cost of ownership and improving availability. The product, which fits with the company's Mission Zero Sustainability Programme, is "a breakthrough in dewatered tailings solutions."
AFP2500 enhancements
With the AFP2500 offering up the prospect of easier media changeout, a new cloth shaking mechanism, cast parts, flexible plate designs, longer media life and more efficient cloth wash systems, there's much for the mining industry to be excited about.
While each of these is noteworthy, FLSmidth's director of tailings solutions, Ken Rahal, points to extension of the media life as being of particular significance in reducing the operating costs of a pressure filter. The new plate design associated with the AFP2500 has the capacity to deliver major benefits on this front.
The result of several years of testing and iteration to determine the source of wear leading to mechanical failure and hence downtime, the plate design has been modified to remove any sharp transition edges, and seen filtrate ports relocated. Additionally, the high-volume wash system for the cloth has been redesigned with redirected nozzles to better wash the target area. The re-design also ensures better alignment with the chamber between the plates across the life of the filter.
These changes have acted to deliver operational enhancements on every cycle and ensure that if high pressure washing is needed, a system has now been designed to do this offline, since high pressure washing of the media inside the filter can take up to an hour and a half each day. That is downtime that has a big impact on the availability of the filter, potentially necessitating further filters.
FLS has also addressed CapEx costs to bring down the TCO by changing the largest metal parts at the head and tail ends from being fabricated to being cast. With casting taking less time and using less steel than fabrication, this has positive cost and emissions implications, while the increased structural integrity and durability reduces downtime. In addition, a simplified cloth shaker system reduces the amount of shaker bar maintenance needed over the pressure filter's operational life.
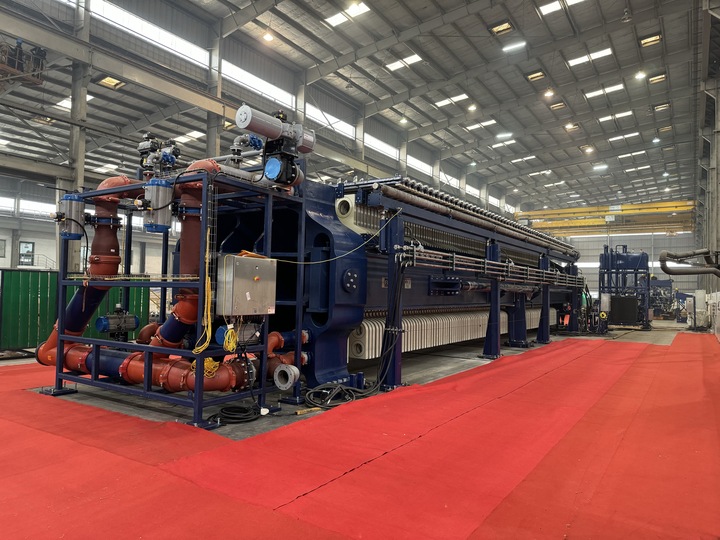
A product for the times
With high profile TSF failures amplifying opposition to large wet impoundments, this has increased the allure of filtered tailings management. Additionally, scarcity of water resources constitutes an ever more important determinant of project feasibility.
Consequently, high efficiency, large-capacity, dewatering equipment, such as the AFP2500, which offers up not only an average of 93% availability, but also up to 95% recovery of process water, will be seen by many as an answer to their prayers. This assists companies in achieving their sustainability objectives and meeting their social license needs.
Rahal explained that while filtered tailings technologies have been available for decades, the process has always been restricted by the size of the filters, which had acted to cap throughputs at no more than 20,000 tonnes per day. And, while larger filters for high-tonnage applications could potentially lower the CapEx, since fewer filters were needed, they were not sufficiently operationally efficient to reduce the OpEx over time. In response FLS's R&D prioritised improving efficiency with a view to reducing the TCO.
In terms of paying quantifiable TCO dividends, Ken Rahal has witnessed mine sites go from 1500 cycles from plate closing to plate opening to upwards of 4500 cycles, equating to three times the media life, which significantly reduces maintenance time and costs.
Digitalised, simplified, optimised
With the AFP2500 marked by data-driven control and decision making for optimised proactive maintenance, this enhanced data-led approach to tailings management could suggest know-how yet unavailable at scale is needed to reap the benefits. Rahal, however, indicated otherwise, given that simplified maintenance procedures should mean less, not more training is needed to develop the necessary skills to operate it.
For example, FLS's Intelliplate turbidity-detecting plate alarm system can detect when and in which chamber mechanical failure of the media has happened so that the issue can be isolated and addressed.
Additionally, the AFP2500's moisture sensor can provide a reading every ten to thirty minutes, depending on the material being filtered, to determine the cake moisture being produced. This provides for near real-time responsiveness to any filter performance issues, and stands in contrast to the pre-digital approach, which saw a once-a-shift sample being taken that would then need to be sent to the lab for analysis before anything could be actioned.
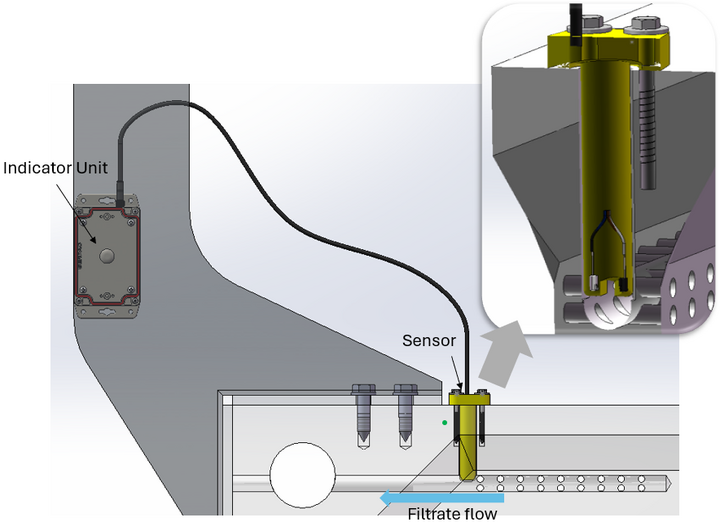
Measurable sustainable benefits
In affording the opportunity to implement filtered tailings even at larger tonnages, FLS is also helping its customers support their sustainability goals and mission statements, and become better community partners. And, at a strategic level, the AFP 2500 actively dovetails with FLSmidth's own Mission Zero Sustainability program, which is centred on zero emissions, zero energy waste and zero water waste.
While filtered tailings are inherently synonymous with recycling as much water as possible, FLS's holistic approach looks at how best to introduce newer technologies upstream in the comminution and processing areas too. Changes made here will have impacts on dewatering within the flow sheet to deliver sustainable benefits.
For example, new technologies in the separations area include the company's patented REFLUX Flotation Cell and CoarseAIR course flotation, which allow customers to increase the grinding size going to filtration, positively impacting dewatering performance and reducing costs attached to thickening. Meanwhile, a happy by-product of a coarser grind is that it improves the geotechnical characteristics of the tailings, whereby the coarse particles provide shear strength for improved physical stability when deposited.
Grinding is responsible for much of the power consumption associated with tailings management. So, quite apart from the cost-reduction implications, the ability to effect a situation where less grinding is needed will be met with enormous interest for its emissions reduction potential from an industry under enormous pressure to deliver sustainable improvements.
A true breakthrough
The AFP2500 has been developed with TCO in mind at every turn. Informed by this approach, FLS has sought to introduce a product that is not only bigger to cope with higher tonnage applications, but more efficient, encompassing simplified maintenance and operational procedures. In this way, an automatic filter press can become a key contributor to bringing costs down across the life of a mine.
A product like that has the potential to supercharge project feasibility.
ABOUT THIS COMPANY
FLSmidth
FLS is a leading, full flowsheet minerals processing supplier to the global mining industry. We deliver proven technologies and services across the lifecycle of operations, and have set targets of providing solutions for zero-emissions mining by 2030 with our MissionZero programme.
HEAD OFFICE:
- FLSmidth A/S Vigerslev Allé 77 2500 Valby, Copenhagen
- Tel: 4536181000
- Website: www.flsmidth.com
- Email: info@flsmidth.com